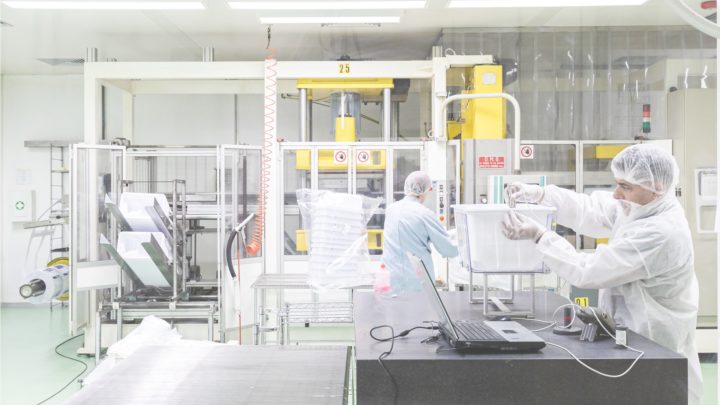
Plastic thermoforming
The Plax Group brings your ideas to life. A complete service that supports all stages of the production process and transforms ideas into finished products.
Vacuum plastic thermoforming
Our plastic thermoforming technology was developed initially in Plax’s headquarters in Bologna. Subsequently, the Turin and Milan offices also integrated this technology, while the Plax offices abroad manage the injection molding.
Our vacuum plastic thermoforming ensures Plax customers a competitive advantage, guaranteed by the application of thevery latest technology in vacuum thermoforming plastics. Thanks to the continuous innovation that distinguishes the Plax Group, we can obtain articles of complex shape at a lower cost; Plax has accumulated extensive experience in manufacturing:
- Trays / plateaus for the internal and external movement of goods;
- Protection devices for industrial processes;
- Box interiors for containers;
- Supports for promotional items;
- Containers for the biomedical sector;
- Transparent clamshell and blister packs for retailers;
- Displays / stands.
The advantages of plastic thermoforming
Plastic thermoforming technology guarantees the possibility of using different materials of varying thickness and colour, depending on the technical requirements and the mechanical or qualitative characteristics of the product to be made.
We could therefore summarize the benefits of plastic thermoforming as follows:
- General advantages of using vacuum plastic thermoforming;
- Flexibility of production quantities;
- Low initial investment for the molds;
- Possibility of molding even large products;
- Use of different thicknesses
- Rapid creation of prototype and final molds
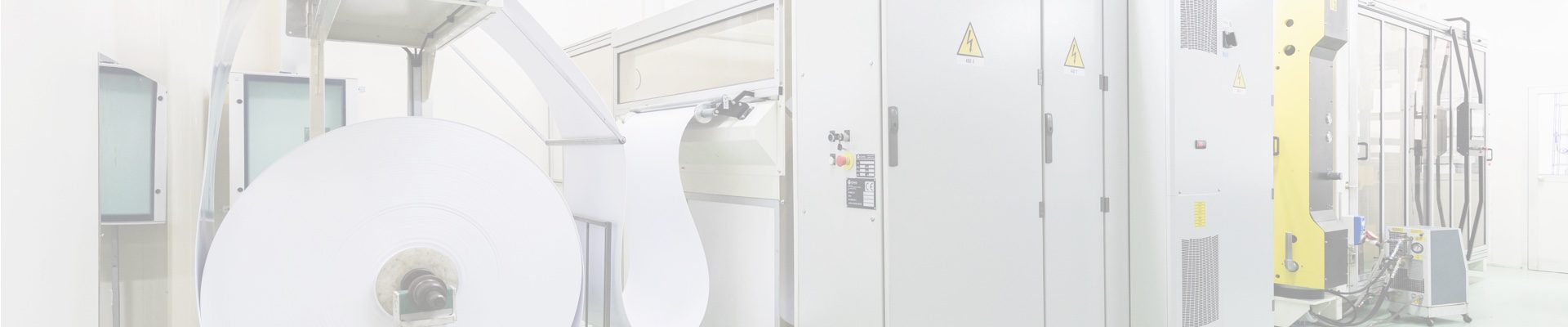
Fields of application of plastic thermoforming
Plastic thermoforming technology is used in various sectors. Plax has extensive experience in the biomedical sector, the retail sector and the industrial sectors, as well as in the manufacture of promotional products.
Plax also offers a series of additional services complementary to the technology.
With reference to the more complex requirements and the technological contents of biomedical products, Plax can produce the primary and secondary packaging containers needed for medical pharmaceutical articles, such as containers for vials, dispensers, applicators, circuit organizers, biomechanical and biocompatible products, products for surgery, vascular prostheses, implantable pulse generators , blisters and trays for surgical kits, for prosthetics in orthopaedics and dentistry and more.
The vacuum plastic thermoforming technique is applied especially when:
- There are specific small-sized elements;
- Packaging is required for objects that are difficult to handle;
- Several preparation steps are involved.
In these cases, Plax purposely produces vacuum thermoformed packaging . The products can be stored without compromising their functionality up until the moment they are used.
Plax manages the production, using plastic thermoforming, of multifunctional containers that can be used in environments such as hospitals, e.g. trays for holding instruments or samples, protective containers for filtering and storage systems.
Technical notes
These products are made using materials with high levels of transparency and purity, so that they are totally non-toxic: they can undergo further sterilization after packaging.
These articles are produced entirely within our ISO 8 certified (class 100,000) clean rooms .
Plax Group produces trays for safe transport for the protection of objects of sizes from 5 mm up to over 500 mm, designed to optimize space and to facilitate all transport operations.
Plax also produces trays for internal handling that can be moved with automatic robotized lines and can be placed on standard plastic containers, transport units, pallets, baskets etc.
Each tray is designed for its depalletization and relative centering auto-fill, by means of a handling system along automatic lines.
These containers can be of varying thickness depending on the objects they have to hold: very thin for single-use trays that will be used in a single transport cycle, or greater thicknesses that allow re-use for multiple cycles.
Plax produces all types of clamshell packages with single or multiple openings, with transparent or coloured materials that can be customized with writing and images, labels or information cards and with possible openings for product testing.
These thermoformed articles can be made with slots for hanging in points of sale; or they can be made with support feet to be placed on flat surfaces.
In addition to clamshell packages, we also make blister packs together with the cardboard insert and the transparent thermoformed shell for anti-shoplifting packages.
The thermoformed shell can be sealed with a cardboard insert or even with plastic sheets welded at high frequency, guaranteeing the airtight packaging of the product .
Plax also produces all the items needed to promote new products on the large retail market.
Some examples:
- Basic supports for promotions in magazines;
- Internal parts for cardboard boxes;
- Internal parts for transparent boxes;
- Internal parts for suitcases;
These products can be customized with coloured labels.
Plax produces these articles using materials that have a strong visual and cosmetic impact, such as flocked materials, which give a velvet effect, materials with a relief effect or combined with other materials and synthetic leather, with controlled opacity or wood effect.
Other processes: Cutting - Assembly - Welding - Painting:
Plax guarantees the provision of ancillary processes, such as the assembly of products made using thermoforming with other products either supplied by the customer or produced in our other factories in Italy, Romania or Tunisia. The additional services offered by Plax are welding, painting and screen printing.
Technical features of Plax thermoforming
The materials that are used for vacuum plastic thermoforming are: PET, PETG, HDPE, ABS, PMMA, ABS-PMMA, HIPS-PC, PP, PVC.
Plastic thermoforming dimensions and thickness
Coil thermoforming
- Maximum size:
- 800 mm x 800 mm (Medical);
- 1100 mm x 1300 mm (Non-Medical);
- Spessori: max 3,0 mm (HIPS only);
- max 1,2 mm (PVC;PET; PETG, PC, HDPE, PP);
Plate thermoforming:
- Maximum size: 2200 mm x 1200 mm
- Thickness: max 10 mm
Machinery fleet
- 18 plastic thermoforming machines
- 4 cutting robots
- Thermoforming in cleanrooms
- ISO 8 certification
Plastic thermoforming and quality control
Plax also uses measuring instruments for the quality control of thermoformed products in terms of size and relative tolerances, thickness, resistance, etc.