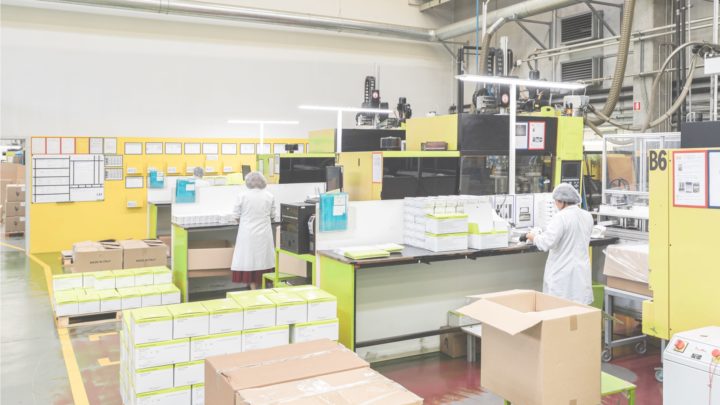
Other services
Alongside plastic molding and design, Plax Group also offers other complementary or additional services, available on customer request.
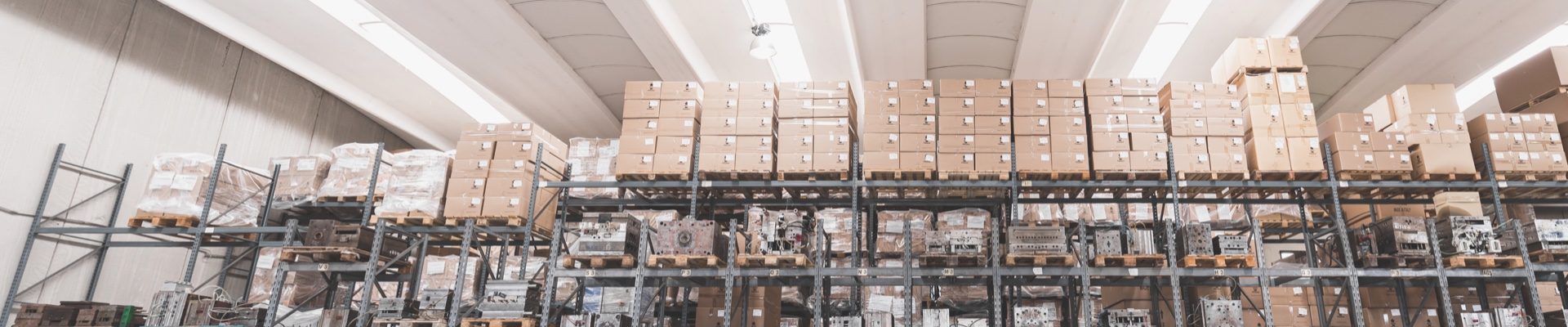
Technopolymers are materials resistant to stress, vibrations, heat and aggressive fluids. Today they are widely used in highly technical industrial sectors, such as the automotive, medical, aerospace, electrical and electronic industries.
Given the vastness of the sector and the high level of applied technologies, the automotive sector is considered one of the most important from a production and economic standpoint.
In recent years, the demand for “light” and “resistant” components has increased in this sector: today, around 16% of the weight of a vehicle is given by plastic, while there are plans to increase this proportion to 25% in the next five years.
A strategic sector from many points of view, the production of molds for manufacturing plastic components for the automotive industry involves both technical and cosmetic components, useful for finishing each item in detail, thus contributing to the construction of a vehicle of excellence. To meet the needs of the world's best automotive brands, Plax follows a well-defined path in the production of high quality molds dedicated to this sector, from the technical drawing to the study of the design of the objects to be made. Finally, if required, Plax also produces the vehicle component needed using injection molding, to be placed on the market.
From the idea to the design
The mold of the requested object is first designed according to the characteristics and needs of the client. The mold is made in the Plax workshops, where it is subjected to quality controls using top-level machinery that is continuously updated technically.
Think plastic, even in the automotive sector
The evolution of the market requires experience and technical know-how in the field of Metal Replacement, an activity in which Plax already boasts recognized expertise, while at industrial level, there have been changes in the technologies used and in the industrialization processes, requiring a general change of attitude as early as the design phase.
Knowledge of polymers in terms of general characteristics, pre- and post-treatment specifications, transformation criteria and process and use behaviour is therefore absolutely necessary.
Fluid dynamics simulation
To obtain an optimal definition, it is essential to use Fluid Dynamics Simulation, first from a product perspective, then from a molding
perspective. The techniques currently available for the 3D printing of objects directly from the model produced using a CAD system,are an excellent solution for this purpose.
Advantages of Metal Replacement
The main advantages of metal replacement are:
- Reduction of Project Time-to-Market,
- Reduction in Raw Material Costs,
- Reduction in Lead Time (fewer phases and more flexibility),
- Performance improvements,
- Strategic product innovation.
From a physical point of view, ultrasonic welding is a high-frequency mechanical vibration applied at a right angle to the coupling surface. In thermoplastic parts, it stresses and creates progressive intermolecular friction that leads to a localized increase in temperature.
This increase, concentrated in an extremely short time interval (in the order of tenths of a second), causes the fusion of a well-defined area (the junction area) which, under the action of a constant force, pushes the two parts together, with each penetrating the other. Therefore, the pieces are welded without the need for glue or additives.
There are many advantages of ultrasonic welding.
The parts can be subjected to other processes immediately after ultrasonic welding. This means that this process is easily included as part of an automation to create a complete production chain, which starts with molding and ends with the finished product.
In addition, there is also the speed of the process, the hermetic seal guaranteed at high pressures, the consistency of results for resistance to torsion and traction, the extreme directivity since only the specific junction area is involved in the process, guaranteeing defined and precise fusion.
Pad printing and screen printing are two printing and colour techniques for plastic parts used by the Plax Group. Screen printing allows you to print on objects of different shapes and sizes, with very short processing times.
Pad printing, a twin technique and very advantageous in terms of quality, transfers the colour through an ink-impregnated pad that comes into contact with the actual piece. The pad printing does not use UV colours and guarantees a very strong adherence to the printing surfaces.
At Plax, we can produce plastic parts in up to six different colours. For decorations requiring more colours, pad printing is the most suitable technique. This also applies to four-colour printing of multiple colours on the same design; moreover, pad printing allows you to decorate with absolute definition irregular surfaces, very small spaces and complex materials.
Thanks to these characteristics, pad printing proves to be an effective printing method and has a wide rang of applications in the cosmetic sector, food fragrance, the automotive industry and electromechanical industry.